DATOS DEL RESPONSABLE DEL AREA
Nombre: Geremias Cárdenas Basurto
Carrera:Ing. Electrica
Semestre: cuarto
No.control: 08401198
Correo: tulittemai_7@hotmail.com
¿ Que es Soldadura ?
La Soldadura es un metal fundido que une dos piezas de metal, de la misma manera que realiza la operación de derretir una aleación para unir dos metales, pero diferente de cuando se soldan dos piezas de metal para que se unan entre si formando una unión soldada.

En la industria de la electrónica, la aleación de estaño y plomo es la más utilizada, aunque existen otras aleaciones, esta combinación da los mejores resultados. La mezcla de estos dos elementos crea un suceso poco comun. Cada elemento tiene un punto elevado de fundición, pero al mezclarse producen una aleación con un punto menor de fundición que cualquiera de los elementos para esto debemos de conocer las bases para soldar. Sin este conocimiento es difícil visualizar que ocurre al hacer una unión de soldadura y los efectos de las diferentes partes del proceso.
El estaño tiene un punto de fundición de 450º F; el plomo se funde a los 620º F. Ver grafica, en este diagrama de proporción de Estaño/Plomo consiste de dos parametros, uno de ellos es la temperatura en el eje vertical y la otra es la concentración en el eje horizontal. La concentración de estaño es la concentración del plomo menos 100. En el lado izquierdo del diagrama puede ver 100% de estaño, en el lado derecho del diagrama puede ver 100% de plomo. Las curvas dividen la fase líquida de la fase pastosa. La fase pastosa de la izquierda de la linea divide el estado líquido del estado sólido. Usted puede ver que estas lineas se unen en un punto correspondiente a una temperatura de 183º C o 361º F, a este punto se le llama punto eutectico. La aleación 63% estaño y 37% plomo tienen la misma temperatura sólida y líquida. Pastoso o en pasta significa que existen ambos estados, sólido y líquido. Entre mas alto sea el contenido de plomo, mayor sera el campo pastoso. Entre mas alto sea el estaño menor sera el campo pastoso. La soldadura preferida en la electrónica es la aleación eutectica debido a su inmediata solidificación.
Diagrama de Fase

Para ver el gráfico seleccione la opción "Descargar" del menú superior
Teoria de Soldadura
Antes de hacer una union, es necesario que la soldadura "moje" los metales básicos o metales base que formaran la unión. Este es el factor mas importante al soldar. Al soldar se forma una unión intermolecular entre la soldadura y el metal. Las moleculas de soldadura penetran la estructura del metal base para formar una extructura sólida, totalmemte metálica.
Para ver el gráfico seleccione la opción "Descargar" del menú superior
Si la soldadura se limpia mientras esta aun derretida, sera imposible retirarla completamente. Se ha vuelto una parte integral de la base. Si unmetal graso se sumerge en agua no se "mojara" no importa que tan degado sea el aceite, se formarán bolitas de agua que se pueden sacudir de la superficie. Si el metal se lava en agua caliente utilizando detergente y se seca con cuidado, sumergiendolo de Nuevo en agua, el liquido se extendera completamente sobre la superficie y formara una pequeña capa. Esta capa de agua no se puede quitar a menos que se seque. El material esta entonces "mojado". Cuando el agua moje el metal entonces esta perfectamente limpio, de tal forma la soldadura mojara el metal cuando las superficies de la soldadura y del metal estan completamente limpias. El nivel de limpieza que se requiere es mucho mayor que con el agua sobre el metal. Para tener una Buena unión de soldadura, no debe de existir nada entre los dos metáles. Casí todos los metáles se oxidan con la exposición al aire y hasta la capa mas delgada impedira que la soldadura moje el metal.
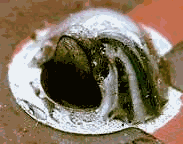
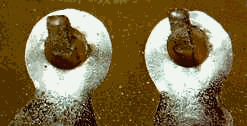
El flux o desoxidante sobrepasa la mayor parte de este problema, como se vera mas aldelante.
Cuando se unen dos superficies limpias de metal y se sumergen en soldadura fundida, la soldadura mojara el metal y subira hasta llenar los espacios entre las superficies contiguas. A esto se le conoce como la acción capilar. Si las superficies no estan limpias, no ocurrira la operación de mojado y la soldadura no llenara la unión. Cuando las tablillas con orificios cromados por una ola de soldadura, es esta fuerza la que llena los orificios y produce un llenado en la superficie superior. La presión de la ola no es lo que produce, esto si no la acción capilar de la soldadura.
Todos hemos visto insectos que caminan sobre la superficie de un estanque sin mojarse las patas. Ellos se apoyan sobre una capa o fuerza invisible llamada tension de la superficie. Esta es la misma que hace que el agua se conserve en bolitas sobre el metal aceitoso. La tensión de la supercie es la capa delgada que se ve sobre la superficie de la soldadura derretida. Los contaminantes de la soldadura pueden incrementar la tensión de la superficie y la mayoria pueden controlarse cuidadosamente. La temperatura de la soldadura tambien afectara la tensión de la superficie, reduciendola al incrementar su temperatura. Este efecto es pequeño comparado al de la oxidación.
Flux
El proposito del flux
- Reduce óxidos en todas las superficies involucrados en la unión de soldadura.
- Reduce la tensión superficial de la soldadura fundida.
- Ayuda aprevenir la reoxidación de la superficie durante la soldadura.
- Ayuda a transferir calor a las superficies a soldar.
Para ver el gráfico seleccione la opción "Descargar" del menú superior
Tipos de Flux
- R – Resina, fue el primer flux utilizado en la electrónica y aun es empleado. Esta hecho de savia que emana de algunos arboles (no haluros/no ácidos organicos). Adecuado para limpieza con solvente/saponificador. Este flux debe de ser lavado.
- RMA – Resina Media Activada (haluros limitados, ácidos orgánicos debiles limiados)Adecuado para limpieza con solvente/saponificador
- RA – Resina Activada (haluros/ácidos orgánicos débiles). Usado por algunos como no-clean, usualmente con solvente/saponificador.
- RSA – Resina Super Activada (alto nivel de haluros y ácidos orgánicos). Limpiado con solvente/saponificador.
- OA – Organico Activado (alto nivel de haluros, alto nivel de ácidos orgánicos fuertes). Debe de ser lavado con agua o saponificador
- NO-CLEAN – Los residuos no se lavan, no degradan la Resistencia al Aislamiento de Superficie (SIR).
NO-CLEAN
RESINA NATURAL Y SINTETICA – Acidos Orgánicos débiles y haluros.
RESINA NATURAL Y SINTETICA – Acidos orgánicos débiles solamente (sin haluros).
VOC-FREE – Acidos orgánicos débiles usualmente libres de resinas. El alcohol es reemplazado por agua.
Soldadura por Ola
Para ver el gráfico seleccione la opción "Descargar" del menú superior
Para ver el gráfico seleccione la opción "Descargar" del menú superior
--- Control de Contenido de Sólidos
- Gravedad Específica
- fluxes de altos sólidos (> 10%).
- Titulación
- Fluxes bajos a medios en sólidos (< 10%).
Los fluxes utilizados en los sistemas sellados no pierden solvente y por lo tanto no requieren de este control.
--- Métodos de Aplicación
- Espuma
- Ola
- Utilizados para fluxes tipo OA, RMA y RA
- Requieren control estricto del contenido de sólidos.
- Spray
-
- Utilizado para fluxes No-Clean.
- SOLDADURAS
Aleación Estándard: 63% de Estaño y 37% de Plomo
La aleación eutectica 63% de Sn y 37% de Pb es una aleación especial donde la fusion ocurre a una sola temperatura que es de 183º C (361º F).
Impurezas Metálicas: Pueden:
- Causar defectos severos de cortos (particularmebte cuando el hierro excede 0.005% y el Zinc excede 0.003%).
- Debilitar la resistencia de la union de la soldadura.
- Incrementar la razón de formación de escoria.
- Causar uniones opacas o granulosas.
- Reducir la capacidad de mojado (particularmente el azufre).
Impurezas No Metálicas: (Oxidos Incluidos).
-
- Las impurezas no metálicas u óxidos inluidos se mojan muy bién en la soldadura fundida y no se separan de la soldadura de la escoria.
- Los óxidos incluidos incrementan la viscosidad de la soldadura fundida, causando cortos y picos (icicles).
- Los óxicos incluidos pueden ser medidos mediante la Prueba de Inclusión de Escoria (Dross Inclusion Test).
- PRECALENTADORES Y OLAS
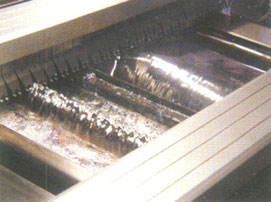
Función del Percalentamiento
- Evapora los solventes del flux (IPA, Agua)
- Previene choque térmico de los PCB y de los componentes.
- Activa el Flux.
- Permite que la soldadura fluya atraves del PCB.
Para ver el gráfico seleccione la opción "Descargar"
Tipos de Precalentadores
- Radiante
- Habilidad pobre para evaporar el agua de los fluxes (VOC Free), pudiéndose generar bolas de soldadura.
- Transparencia de calor selectiva.
- Convección Forzada
- Alta eficiencia en transparencia de calor.
- Volatiza el agua de los fluxes (VOC Free).
- Minimiza el incremento de temperatura entre las areas del PCB.
Tipos de Ola
-
Ola laminar usada en PCB de Throuh – Hole.
- Simple (Laminar)
- Doble (Laminar/Turbulenta).
Ola turbulenta seguida de ola laminar usada en PCB con componentes de SMT en el lado de la soldadura. La ola turbulenta previene el efecto de sombra en los componentes.
Para ver el gráfico seleccione la opción "Descargar" del menú superior
- SISTEMAS INERTES (Nitrógeno)
Beneficios
- Previene oxidación.
- Facilita el uso de fluxes No-Clean.
- No decolaración en los PCB.
- Reduce la formación de escorias
- Menos mantenimiento requerido.
- Menos soldadura utilizada.
- Menos escoria que disponer.
Tipos de Sistemas Inertes (con Nitrógeno).
- Sistema de Túnel Inerte
- Ambiente inerte en precalentadores y ola.
- Consumo de nitrógeno: 1400 – 2400 CFH.
- Sistema Inerte Limitado.
-
- Ambiente inerte solo en la ola
- Consumo de nirógeno: 300 CFH.
- PARAMETROS DEL PROCESO
Orientación de la Tarjeta.
- Los conectores e IC’s deben viajar perpendicularmente a la ola. Los chips deben de viajar paralelamente a la ola.
Flux.
- Verifique que el flux séa aplicado uniformemente en el PCB.
- Seleccione un flux adecuado al proceso. Si se requiere el uso de la ola turbulenta el flux debe sobrevivir mayor tiempo en contacto con la ola de soldadura.
Velocidad del Coveyor.
- El tiempo de contacto con la ola es función de la velocidad del conveyor y el area de contacto con la ola.
- Ajustar la velocidad del conveyor de acuerdo al tiempo de contacto especificado (Típico: 1.5 – 3.5 seg.)
El tiempo de contacto es el acumulado entre las olas turbulentas y
laminar.
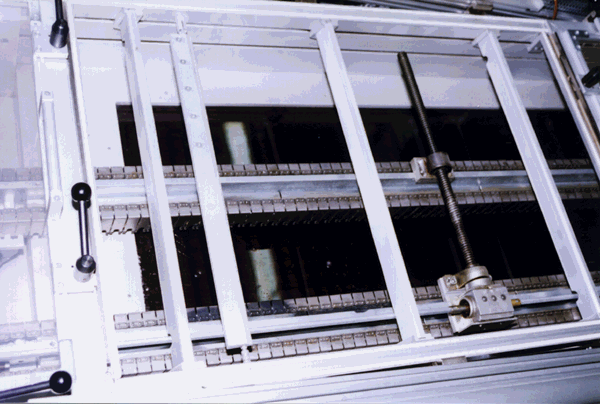
Para ver el gráfico seleccione la opción "Descargar" del menú superior
Precalentamiento.
- Precalentar tan rápido como séa posible pero sin exceder 2ºC/Segundo, medido en el lado superior de la tarjeta. Exceder 2ºC/Segundo (3.5ºF/Segundo) puede causar daño a los componentes debido a choque térmico.
- Fluxes VOC Free.
- Es optimo llevar la mayoria de los fluxes VOC Free hasta los 105-120º C (220º- 250º F).
- Temperaturas inferiores pueden resultar salpicaduras.
- Temperaturas superiores pueden volatilizar prematuramente los activadores causando defectos de cortos de soldadura.
Temperatura del Crisol.
- El rango recomendado es de 460 – 500º F (235 – 260º C).
- El uso de dos olas limita la actividad del flux. Use la ola turbulenta solo si tiene componentes de SMT en el lado de abajo del PCB.
Contaminación y Controles
La pureza de la soldadura tiene una gran efecto en la parte terminada y el numero de rechazos. Por consiguiente entender los efectos de la contaminación de la soldadura obviamente nos puede llevar a mejorar la calidad de las partes producidas a un costo reducido. Se recomienda no ignorar los efectos perjudiciales de las impurezas de la soldadura en la calidad y el indice de produccióndel equipo de soldadura por inmersión o de onda. Algunos de los problemas que prevalecen a causa de soldadura contaminada son uniones opacas o asperas, puentes y no poderse "mojar". Cambiar la soldadura no es necesariamente la solución. Las soldaduras se pueden dividir en tres grupos básicos:
1).- Soldadura Reciclada
2).- Virgen.
3).- Alto Grado de Pureza.
Soldadura reciclada es desperdicio de Estaño y Plomo que se puede comprar y refinar por medio de procedimientos metalurgicos regulares. Los altos niveles de impureza pueden provocar problemas en las lineas de producción en masa. Soldadura Virgen este termino se refiere a la soldadura que estan compuestas de Estaño y Plomo estraidos del mineral. El nivel de pureza del Estaño y Plomo de esta materias primas es alto y excede, en muchos aspectos de la magnitud y las normas (ASTM & QQS-571). Soldadura de alto grado de pureza se selecciona Estaño y Plomo con bajo nivel de impurezas y se produce soldadura con bajo nivel de impurezas.
Antes de discutir problemas y soluciones considere la fuente de la contaminación metálica en un crisol u onda durante la manufactura. Obviamente en una parte del equipo bien fabricada, las paredes del recipiente para el metal fundido, al igual que la bomba y todas las demás superficies que llegan a estar en contacto con la soldadura estan hechas con un metal como el acero inoxidable. La contaminación del baño, por consiguiente, puede resultar unicamente por el contacto con el trabajo mismo.
Esto significa que un numero limitado de elementos se adquieren, dependiendo de la linea de producción. En el crisol de inmersión, esto significa que se podra encontrar cobre y zinc, al soldar con ola ensambles electrónicos y tablillas de circuitos impresos, significa que se podra encontrar cobre y oro. En otras palabras, un baño de soldadura solo se puede contaminar con aquellos metales con los que esta en contacto y los cuales son solubles en la soldadura.
Al ir subiendo el nivel de contaminación, la calidad de la soldadura se deteriora. Sin embargo, no existe una regal clara en cuanto al nivel de contaminación metálica donde la soldadura ya no se puede emplear.
No podemos prevenir que los materiales de los PCB toquen el baño e inevitablemente contaminaran la soldadura hasta cierto grado. No existen valores absolutos para todas las condiciones. El limite depende de los requisitos de especificación, diseño del PCB, solderabilidad, espaciado de los circuitos, tamaño de los conectores y otros parametros. Establezca sius propios niveles de contaminación.
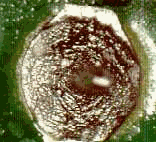
Los Efectos de Contaminantes Comunes
Cobre
|
Uniones con apariencia arenosa, la capacidad de mojarse se ve reducida.
|
|
Aluminio
|
Uniones arenosas, aumenta la escoria en el crisol.
|
Cadmio
|
Reduce la capcidad de mojado de la soldadura, causa que la unión se vea muy opaca.
|
|
Zinc
|
Provoca que el indice de escoria aumente, las uniones se ven escarchadas.
|
|
Antimonio
|
En cantidades arriba de 0.5% puede reducir la capacidad de mojarse de la soldadura. En pequeñas cantidades mejora la capacidad de baja temperatura de la unión de la soldadura.
|
|
|
|
Hierro
|
Produce niveles excesivos de escoria.
|
Plata
|
Puede provocar uniones opacas, en concentraciones muy altas hara que la soldadura sea menos movil. No es un contaminante malo. Se añade a algunas aleaciones en forma deliberada.
|
|
|
|
Nickel
|
En pequeñas concentraciones, provoca pequeñas burbujas o ampollas en la superficie de la unión.
|
|
Nota: La union de la soldadura tiene apariencia opaca. El antimonio elimina este efecto.
OTROS CONTAMINANTES
Fosforo, Bismuto, Indio, Sulfuro, arsenico, etc. Algunos de estos pueden considerarse contaminantes, sin embargo, unos de ellos se añaden a la soldadura en forma deliberada para fines especiales. Para soldar las tablillas a máquinas, se consideran materiales que pueden provocar contaminación de las uniones.
La escoria es el óxido que se forma en la superficie de la soldadura. El indice de la generación de escoria depende de la temperatura y la agitación. Mucho de lo que aparenta ser escoria es, en realidad, pequeños globules de soldadura contenidos en una pequeña pelicula de óxido. Entre mas turbulenta sea la superficie de la soldadura, mas escoria se produce. Los contaminantes tambien juegan un papel importante en la formación de escoria. Los elementos que oxidan contribuyen a esta formación. Aunque se cree que la escoria es perjudicial en los procesos de soldadura de ola, el óxido de la superficie protéje contra oxidación futura. No es necesario quitarla escoria con frecuencia, unicamente si interfiere con la acción de la ola o si la ola consiste en escoria.
Quitar la escoria una vez al día es, por lo general suficiente. Las areas donde se puede controlar la escoria son la temperatura y la agitación. Se ha encontrado que lo que se considera escoria es una mezcla de compuestos intermetalicos y escoria. Es importante quitar la acumulación superficial del crisol con herramientas que permitan que el metal se vuelva al crisol y solamente se quite la escoria. Se han empleado muchas cosas para reducir la escoria, pero mientras haya exposición al oxigeno, se generara escoria.
PERFILES TERMICOS
Para ver el gráfico seleccione la opción "Descargar" del menú superior
Este asegura que el proceso por soldadura de ola este en control. El analizador térmico es una herramienta de medición (Temperatura VS Tiempo) y detecta los cambios que presenta en proceso de soldadura en la máquina.
PERFIL
Esta definido como el traza un gradiente térmico por unidad de tiempo.
Los perfiles térmicos analizan:
- Cuantifican los Parametros de los Precalentadores
- La Temperatura de la Ola.
- El Paralelismo.
- Tiempo de Contacto (Tiempo de Contacto como la Velocidad del Conveyor).
Para ver el gráfico seleccione la opción "Descargar" del menú superior
Tabla de Diagnóstico
Cortos
- Flux insuficiente.
- Precalentamiento fuera de especificación.
- Orientación de PCB Incorrecta.
- Soldadura contaminada.
- Temperatura del crisol baja.
- Altura de la ola incorrecta.
- Escoria de la ola.
- Ola desnivelada.
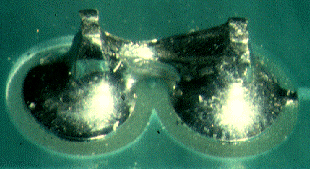
Insuficiencias
- Relación alta de hoyo a terminal.
- Altura de ola incorrecta.
- Ola desnivelada.
- Soldabilidad PCB/Componentes.
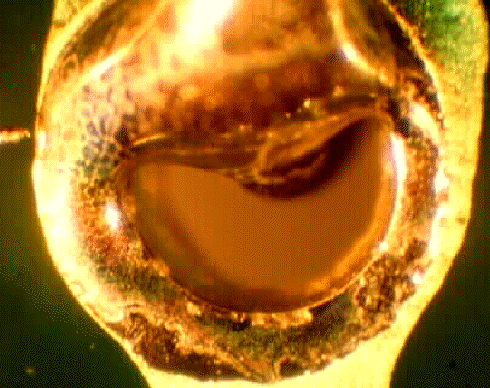
Bolas de Soldadura
- Precalentamiento fuera de especificación.
- Tipo de mascarilla.
- Flux insuficiente.
- Tiempo de contacto excesivo.
- Uso de ola turbulenta.
- Pobre calidad de PTH (Fractura en Pared).
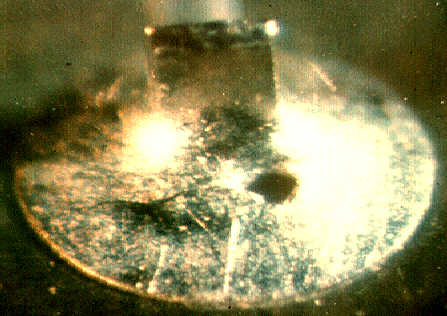
Bibliografia
Manual de Alpha-Fry Technology
A cook Electronic Company.
U.S.A. 2002
Manual de Soldadura de Omega.
Soldaduras Omega S. A. de C.V.
México 2000
Circuits Assembly
www.circuitsassembly.com
www.iupui.edu/~eet360/m200_wave.htm
www.thepdfshop.co.uk/ppm/asp/wave.asp
A CONTINUACION LES FACILITARE UN PROCEDIMIENTO PARA FABRICAR UN GENERQADOR PEQUEÑO PARA CARGAR BATERIAS
Este capítulo describe cómo fabricar un generador de imanes permanentes (GIP). Este generador puede ser llamado asimismo un alternador ya que produce corriente alterna (AC). No puede generar electricidad de la tensión de red, pues su voltaje es bajo y de tres fases. La corriente AC es cambiada a DC para cargar baterías.
Este GIP consiste de:

En el diagrama que antecede se pueden apreciar los componentes descritos.
El estator contiene seis bobinas de alambre de cobre y está vaciado en la resina que se emplea con la fibra de vidrio. Este estator está montado al tope y no se mueve. La electricidad que se toma de las bobinas se lleva a los rectificadores, que transforman la AC a DC para cargar baterías. Los rectificadores están montados sobre disipadores de calor.
Los rotores con los imanes están montados sobre municioneras (Preferiblemente que toleren impulsos laterales, o sea cónicas), que giran sobre el eje. El rotor trasero está detrás del estator y embutido dentro de él. El rotor frontal está del lado exterior del estator y fijado al posterior por pernos largos que pasan por un agujero en el centro del estator. Las aspas de la turbina se colocarán sobre estos mismos pernos.
Las aspas harán girar los rotores, que a su vez harán pasar los imanes sobre las bobinas. El flujo magnético de un rotor pasará al otro a través de las bobinas. Este flujo magnético produce electricidad.
Es aconsejable que antes de comenzar lea este capítulo en su totalidad para entenderlo bien.
La sección 2 es una lista de los materiales requeridos para construir este GIP.
La sección 3 explica cómo construir algunas herramientas y moldes que se requieren. Con ellas se pueden construir varios GIPs.
La sección 4 habla sobre el estator. Describe como hacer las bobinas y vaciarlas en resina usando las herramientas y moldes de la sección 3.
La sección 5 explica como fabricar los rotores empleando imanes y discos de acero también vaciados en resina.
La sección 6 describe cómo armar el conjunto en un GIP. Explica cómo armar sus partes mecánicas, balancear los rotores y el cableado del estator.
La sección 7 describe cómo probar el GIP. Describe procedimientos para el balanceo final del conjunto y ponerlo listo para su uso con las opciones de cablearlo para aprovechar su capacidad máxima de generación. También explica cómo conectarlo a una batería.
QUE PUEDE HACER ESTE GIP
Este GIP es pequeño. Además del generador mismo se necesita:
-
Una torre, posiblemente hecha de tubos y apoyada en vientos de alambre.
-
Una plataforma u otro elemento rotatorio en el tope de la torre
-
Una veleta que haga que el generador siempre esté de frente al viento
-
Un juego de aspas.
El tope del GIP se fija al elemento rotatorio. Las aspas van al frente del GIP.

Este GIP trabaja a bajas velocidades. La tabla que sigue muestra sus capacidades de carga a una batería de 12 voltios. Girando a 420 RPM genera 180 vatios (O sea, 15 amperios a 12 voltios). A mayores velocidades genera más electricidad pero esta calienta las bobinas, lo que induce ineficiencias. Esto se puede resolver empleando alambre de mayor diámetro en las bobinas o variando su cableado. Si las corrientes de viento de su localidad son rápidas constantemente esto no es problema, pues al usar alambre de mayor diámetro y un menor número de vueltas en sus bobinas el generador no funcionará a bajas velocidades.
Para usar éste GIP tanto a bajas como a altas velocidades es posible cambiar sus conexiones. Existen dos métodos, el "estrella o Wye" y el "delta". La sección 7 detalla estas conexiones. La conexión estrella es buena a bajas velocidades y la delta a altas.
El gráfico que sigue muestra la generación en relación con la velocidad de giro del GIP. La configuración estrella comienza a generar a 170 RPM.

Una versión mayor de este GIP dará mayor potencia a menores revoluciones
-
Al armar los imanes asegúrese que no pueden desprenderse de su sitio. En circunstancias extremas la fuerza centrífuga puede despedirlos de su sitio si no están bien fijados, dañándose así el GIP.
-
Siga cuidadosamente las instrucciones al vaciar los rotores de los imanes. No se trata sólo de engomarlos a los discos metálicos.
-
No golpee los imanes con martillos en ningún momento.
-
Debe haber no menos de 1mm de distancia entre los imanes y el estator. A altas velocidades permita que esta distancia sea algo mayor.
-
El GIP no debe girar a más de 800 RPM. (Cuando la turbina gira se desarrollan altas fuerzas giroscópicas que doblan el eje siendo posible que los imanes toquen el estator.
-
No coloque las aspas sobre el disco del rotor. Colóquelo sobre los pernos que atraviesan ese disco.
-
El tope del GIP debe quedar vertical.
|
|
|
|
Unidades
|
Peso en Kg.
|
SUMINISTROS DE FIBRA DE VIDRIO
|
|
|
|
Resina (mezclada con el acelerador)
|
|
|
2,70
|
Catalista (peróxido)
|
|
|
|
0,05
|
Talco
|
|
|
|
|
1,20
|
Fibra de vidrio
|
|
|
1 m cuadrado
|
Mastique
|
|
|
|
|
|
ACEROS
|
|
|
|
|
|
Alambre de acero inoxidable
|
|
2mm x 10m
|
|
IMANES
|
|
|
|
|
|
Imanes de ferita grado 3
|
|
|
16
|
|
ELECTRICOS
|
|
|
|
|
Alambre de cobre para bobinas 14 AWG
|
|
|
3,00
|
Alambre de cobre para bobinas 14 AWG
|
|
6 metros
|
|
Soldadura de estaño
|
|
|
|
|
Cinta eléctrica de 1/2"
|
|
|
|
|
Rectificadores 25A 200W una fase
|
|
2
|
|
Disipador de calor
|
|
|
|
|
ACEROS
|
|
|
|
|
|
Tubo para el tope (380x50x525)
|
|
1
|
|
Discos para los imanes (6mmx305mm diámetro)
|
2
|
|
Barra de 10mm roscada
|
|
|
1 metro
|
|
Tuercas de 10 mm
|
|
|
32
|
|
Arandelas de 10mm
|
|
|
16
|
|
Barra roscada de 8 mm
|
|
|
400 mm
|
|
Tuercas de 8mm
|
|
|
8
|
|
Tornillos y tuercas de 5mm x 20mm para los rectificadores
|
2
|
|
Eje (25mm x 150 mm
|
|
|
|
|
MECANICOS
|
|
|
|
|
Rolineras (sección 6)
|
|
|
1
|
|

Materiales para las herramientas y moldes
En esta sección se explica cómo hacer las herramientas y moldes para fabricar el GIP. Estas herramientas son útiles para fabricar otros GIPs adicionales.
MAQUINA DE BOBINAR


-
1. Más adelante le indicaremos el diámetro del alambre y cuántas vueltas debe llevar cada bobina. En este momento lo que usted necesita es una herramienta sencilla que le permita bobinar veinte bobinas de treinta vueltas rápidamente, cada una siguiendo más o menos la misma forma. En este capítulo le explicamos cómo puede fabricar uno. La salvedad es que si decide posteriormente fabrican otro generador con bobinas diferentes una pieza de este aparato no le sirve, pues sus medidas se adaptan a este caso en especial.

Corte tres trozos de 15 mm de madera como los que se indican

Al alinear esta tres piezas como lo indica el diagrama tendrá un fabricador de bobinas cuadradas de esquinas redondas. La pieza central de madera es la que le dará la forma deseada a sus bobinas y la que deberá reemplazar si debe hacer otras diferentes.

Las pestañas debajo de la bobina son para insertar cinta adhesiva que envolverán sus bobinas al retirarlas del molde.

Consiga los apoyos de su manivela y está Ud. listo para bobinar. Observe Como habrá de efectuar este proceso en el diagrama.

MOLDES PARA FABRICAR LOS ROTORES
Los imanes de los rotores se montan sobre una plancha de metal. Como Ya hemos mencionado, la fuerza centrífuga puede causarnos problemas. Estos no los podemos evitar. Pero sí que los imanes de desplacen a causa de esa fuerza. Solo basta con tallar (A torno) una canal en la que se puedan insertar los imanes. La canal estará centrada en el DCP (Diámetro del Círculo de Paso) de los imanes .Además de asegurarnos que quedan todos distanciados exactamente del centro del GIP evitamos que la fuerza centrífuga los desprenda.

Herramientas para fabricar los rotores.
PLANTILLA DEL DCP.
La plancha de acero de que hemos hablado tiene varios agujeros. La nuestra tiene cuatro agujeros a un DCP de 102mm (4 pulgadas). Usted decide el arreglo de esos agujeros. Nuestra plantilla será la que usaremos para perforar esos agujeros y balancear nuestros rotores. Los agujeros deben ser marcados y taladrados con mucha precisión.

El proceso es el siguiente:
-
Corte un pedazo de plancha de 125mm por 125mm.
-
Trace líneas diagonales desde las equinas de esta plancha. Marque lo más exactamente que pueda el punto de cruce de las diagonales con un centro punto.
-
Abra un compás a un radio de 51mm y trace un círculo desde el cruce de diagonales. Marque con un centro punto los cruces de las diagonales con el círculo.
-
Abra ahora el compás a un radio de 72 mm. Marque nuevamente los puntos de cruce de las diagonales con el nuevo círculo.
-
Ahora puede hacer sus agujeros.
PLANTILLA DE UBICACIÓN DE LOS IMANES

Con esta plantilla posicionaremos los imanes en sitios correctos en las planchas de acero. Solo necesitamos una, que podemos hacer sobre una plancha de 250x250 mm de madera o aluminio. No se debe usar acero.
-
Busque y marque el centro del material.
-
Trace tres círculos de 50, 102 y 200 mm diámetro desde el centro.
-
Trace dos tangentes paralelas al círculo de 50 mm
-
Trace dos pares de tangentes paralelas más a éste círculo, uno a 45 y otro a 90 grados del primer par.
-
Marque las posiciones de los imanes y corte la plantilla como se indica.
-
Trace una línea que conecte los centros de las bases de dos imanes opuestos entre sí.
-
Coloque la plantilla de DCP que habíamos fabricado sobre el círculo de 102 mm y marque los cuatro agujeros de ésta plantilla.
MOLDES
Los moldes se usarán para vaciar el estator y los rotores. Pueden hacerse también de madera o aluminio.
Sobre estos moldes se vaciarán las piezas que necesitamos usando fibra de vidrio. La superficie de cada molde debe ser perfectamente planas, robustas y lisas. A veces resulta difícil separar el vaciado de los moldes y se requiere martillarlos para separarlos. Puede resultar útil tener una bobina a mano para verificar que quepa en su sitio del vaciado.
A seguidas describimos un método de fabricar estos moldes empleando láminas de madera

Corte varias ruedas de madera de aproximadamente 500 mm de diámetro por 20 mm de espesor.
Deje un disco aparte. A los demás, córteles un círculo de 360 mm de diámetro de manera de formar unos anillos de madera.

-
Marque el centro del disco que reservó y coloque los anillos sobre él. Encólelos formando una pila de anillos con un agujero de 60 mm de profundidad.
-
Corte un pequeño disco de 140 mm de diámetro y encólelo al centro de la pieza anteriormente preparada.

-
De lo que se trata ahora es de pulir la parte interna del molde. Esto se puede hacer a torno de madera o a motor haciendo un porta disco. El porta disco consiste en un pedazo de madera (Tenemos varios) con un agujero en su centro. El disco engomado se fija a este pedazo por su base y se monta sobre el motor o el torno. Ahora, con una cuchilla, se pule el molde. Tenga cuidado de que el molde está alineado en su eje central.

ACABADO DEL MOLDE
-
Las paredes de los anillos tienen un bisel de aproximadamente 7 grados. De esa manera el vaciado sale más fácil del molde.
-
El diámetro de la cara plana es 380 mm
-
El diámetro del borde exterior es 360 mm
-
En el fondo no debe haber aristas, sino una curva leve.


-
Si la bobina no cabe en el sitio para ello, haga el disco central más pequeño. El centro de la bobina debe quedar a 250 mm del centro del molde.
-
Para terminar, divida con un lápiz el fondo del molde en seis campos de 60 grados cada uno.
AGUJEROS DEL MOLDE
Perfore cuatro agujeros en el lugar del centro que separa los dos moldes.

Inserte varillas de madera en esos agujeros para fabricarles patas al molde.
MOLDE INTERIOR DEL ESTATOR

-
Se trata de discos de madera de 370 mm de diámetro.
-
Perfore un agujero de 12 mm en el centro del cada uno.
-
Encólelos en una pila de 45 mm, mejor si es de 50 mm.
-
Hágale un bisel de 20 grados en el costado y redondee las aristas de manera que diámetro reduzca de 368 a 325 mm.
-
Verifique que el molde externo encaja con el interno dejando una luz de 6 mm a lo largo de su filo.
-
Trace dos líneas a una distancia de 340 mm entre ellas sobre la cara del molde.

-
Corte dos caras planas en los lados marcados como aparecen en el dibujo.
-
Estas caras harán que el molde sea más ancho en el sitio por donde van los pernos de montaje.
-
Se necesitan dos vaciados de este molde, a menos que haga dos moldes.
MOLDE DEL ROTOR
Este molde es similar al del estator, pero más sencillo.

Use la plantilla del DCP para perforarle los cuatro agujeros de las planchas de imanes.
Cada molde del rotor requiere de un disco interno con el mismo patrón de cuatro agujeros.

Todos los moldes deben ser lijados para lograr una superficie plana. Deben sellarse con poliuretano y pulirse.

Molde siendo fabricado y luego usado
Plantillas para el estator.
Plantilla De los pernos del stator.

Junto con el estator hay que vaciarle cuatro pernos. Esta plantilla se requiere para sostenerlos mientras la resina endurece. Esta plantilla es de madera de 380 X 50 X 25 mm. Tiene que ser exacta o los pernos no encajarán en el tope posteriormente.
-
Marque el centro exacto de la cara más larga.
-
Use un compás o un calibrador para hacer un arco a un radio de 178 mm de esta marca.
-
Haga cuatro marcas en estos arcos a 30 mm de distancia y a 10 mm del borde
-
Perfore agujeros de 8 mm.
PLANTILLAS DE PAPEL O CARTULINA
La fibra de vidrio se debe cortar siguiendo estas plantillas

Esta sección explica cómo se construye el estator empleando las plantillas y moldes de la sección 3. Será prudente disponer de una bobina antes de fabricar los moldes para verificar su ajuste adecuado.
Bobinado
-
El rollo de alambre de las bobinas debe estar alineado con la herramienta de fabricarlas.
-
Deje un cabo de 100 mm y doble el alambre a 90 grados solamente en el sitio donde comienza la bobina y no en otro lugar. El alambre doblado no permite fabricar bobinas compactas.
-
Tome el alambre con un pedazo de trapo para que lo mantenga tenso.
-
La primera vuelta empieza en el filo por donde el extremo del alambre escapa del bobinado. Las demás vueltas deben ser ordenadas sin pisar el alambre. Construya la bobina en capas ordenadas. Cuente cuidadosamente el número de vueltas. Normalmente sólo serán 100.
-
Al terminar, deslice un pedazo de cinta adhesiva por debajo del centro de la bobina y presiónelo fuertemente. No corte el alambre hasta que haya hecho esto. Deje un cabo de 100 mm proyectándose de la bobina.
-
Coloque las bobinas de modo que todas estén iguales. El cabo de inicio del bobinado debe quedar arriba.
-
Numere las bobinas del 1 al 6.


Bobinas 1 y 6 - 800 mm
Bobinas 2 y 5 - 600 mm
Bobinas 3 y 4 - 400 mm
-
Cubra los empates muy bien no deje metal a la vista.
-
Identifique cada cabo con las letras A y B. El cabo A es el de inicio de la bobina y el cabo B el del final.
-
Coloque las bobinas en el molde externo.
-
Verifique que caben cómodamente y que sus cables están dentro del molde hasta su punto de salida entre las bobinas 3 y 4.

PREPARACIONES PARA VACIAR EL ESTATOR
El vaciado del estator contiene:
-
Seis bobinas
-
Resina y talco (Si lo desea algún pigmento de color)
-
Fibra de vidrio
-
Cuatro pernos roscados de 8mm x 100mm
-
Esté seguro de tener los moldes listos. Rocíeles silicona (Viene en potes de spray)..
Corte la fibra de vidrio usando la plantilla correspondiente. Habrá dos discos circulares a tender planos en el molde externo. Necesitará también recubrir los laterales del molde con dos capas de fibra. Permita un solapamiento de 25 mm entre tira y tira de fibra.
Al estar seguro de tener todo listo puede iniciar el proceso de vaciado. Sería buena idea leer todo el procedimiento primero para entenderlo. En la Sección 8 hay algunas notas relativas a ese procedimiento.
Procedimiento de vaciado

El talco se usa para evitar el recalentamiento de la mezcla. No es necesario si se va a mezclar una cantidad pequeña.
MEZCLA DE LA RESINA DE POLIÉSTER.
Mezcle bien la resina y el catalizador, aunque lentamente para impedir la formación de burbujas de aire. Añada el talco sólo al mezclar el catalizador. Use toda la resina de una sola vez, pues al quedar mezclada se calentará y fraguará. Use solamente la cantidad exacta de catalizador. Los vaciados de resina no requieren tanto catalizador como el trabajo normal de fibra de vidrio (Aproximadamente la mitad). Si tiene dudas, haga algunas pruebas. No tardan tanto.
Aplique la resina en una acción de "empuje".
-
Coloque el molde sobre papeles de periódico sobre un banco de trabajo.
-
Mezcle 200 gramos de resina con 3 centímetros cúbicos de catalizador. No use el talco todavía.
-
Pinte con esta resina todo el interior del molde exterior. No pinte la parte superior de la isla central.
-
Coloque una capa de fibra de vidrio en todo el interior del molde y píntela también. Evite las burbujas de aire o elimine las que hayan en la capa de fibra.
-
Coloque la segunda capa de fibra y píntela nuevamente.
-
Coloque las bobinas en el molde. Tenga cuidado con el espacio que cada una ocupará. Sus cables saldrán del molde en un solo lugar entre las bobinas 3 y 4.
-
Mezcle otros 100 gramos de resina con 2cc de catalizador. Vacíe esta mezcla sobre las bobinas. Evite hacer "pozos" dentro de ellas.
-
Mezcle otros 600 gramos de resina y 9cc de catalizador y 600 gramos de talco. Vacíe esta mezcla en los espacios entre las bobinas. La resina debe llenar el molde hasta que esté a nivel con la isla central.
-
Sacuda el molde vigorosamente para eliminar las burbujas de aire.
-
Mezcla otros 200 gramos de resina y 3cc de catalizador y 100 gramos de talco. Coloque el último disco de fibra sobre las bobinas y píntela con resina.
-
Coloque el molde interior dentro del exterior y coloque el perno de 12 mm a través del centro de ambos.
-
Acomode los cables en el espacio entre los moldes. Una de las partes planas del molde interior debe quedar en el sitio donde los cables salen del estator. La resina subirá de nivel. Es posible que desborde el molde.
-
Si es necesario, vacíe resina en el espacio entre los moldes hasta que el nivel suba a nivel del molde femenino. Puede necesitar otros 100 gramos de resina y 1.5 cc de catalizador. Tome nota de las cantidades de resina y catalizador utilizador por si se presenta una segunda oportunidad de hacer otros vaciados.
-
Coloque la plantilla para los pernos sobre el molde interno con un extremo sobre los cabos de cable. Apriete el perno de 12 mm con una tuerca e inserte los pernos de 8 mm con tuercas por arriba. Los pernos deben estar sumergidos en la resina por una longitud aproximada de su mitad.

Seis pasos del procedimiento de vaciado
ELEMENTOS DE VACIADO DEL ESTATOR


Este proceso ha concluido. El vaciado se calentará y fraguará en algunas horas. Para acelerar el proceso, si lo cree necesario, colóquelo en un sitio caliente.
Cuando la resina haya endurecido saque el vaciado del molde. Tenga paciencia y no maltrate los moldes. Saque la plantilla de los pernos. Separe los dos moldes golpeando levemente algunos pernos que insertará en el molde central.
El rotor de imanes también es un vaciado. Más adelante describimos un procedimiento para armarlo. Reúna las planchas metálicas, imanes, alambre de acero inoxidable, etc.
Planchas metálicas.
Cada rotor se construye sobre una plancha de acero de 6mm. No use aluminio ni acero inoxidable para estos discos, ya que deben ser material magnético. Estos discos tienen agujeros para montar el espaciador. En nuestro caso son cuatro agujeros, cada uno de 10 mm en un círculo a 102 mm (O 4 pulgadas) al centro de los agujeros. Si se usara un espaciador diferente, todos los moldes deben casar con él.

En el centro del disco hay un agujero de 65mm. Deben haber cuatro agujeros roscados para las barras de 10 mm a 220mm del DCP. Estas barras se embutirán a la resina para unir el vaciado al disco.
Las planchas deben ser planas. Si no es posible cortarlas sin doblar las planchas, use una guillotina y corte un octágono con una longitud de 116mm entre lados opuestos

Limpie hasta que brille y quite la grasa que haya sobre la plancha antes de colocarla en el molde para vaciarle la resina.
Imanes.
En cada rotor se colocan ocho imanes. Cada imán tiene un polo positivo (O norte) y un polo negativo (O sur).

Tenga cuidado al manipular los imanes. Le pueden dañar discos de computador, cintas musicales, tarjetas de crédito y de cajeros bancarios automáticos. Algunos son tan fuertes que al atraerse golpean pudiendo quebrarse. Por ello no se deben usar martillos para ajustar un imán en su sitio.
Las caras de los imanes sobre los discos deben alternar sus polos N-S-N-S. Para verificar esa colocación haga que el manual que sigue repele al anterior. O márquelos a partir de un primer imán al cual se le puso arbitrariamente "N" y "S" en sus caras.

COLOCACIÓN DE LOS IMANES.
Los dos rotores deben atraerse mutuamente cuando los imanes han sido debidamente alineados. Esto se verifica por los agujeros del rotor. Gire uno de los rotores hasta que la atracción ocurra.

ALAMBRE DE ACERO INXIDABLE
Cuando el rotor esté girando, los imanes tratarán de escapar de su sitio por causa de la fuerza centrífuga. Si no ha tallado la canal en su plancha de acero, la resina puede no resultar tan resistente para contener los imanes. El refuerzo consiste en un anillo de alambre de acero inoxidable alrededor de los imanes. El acero inoxidable es antimagnético y lo puede conseguir con cualquier pescador.
La otra alternativa es tallar una canal en el disco de un par de milímetros y colocar los imanes dentro de ella. Esto nos garantiza fijación y precisión de colocación de los imanes y nos permite prescindir del anillo de alambre.
Antes de usar la resina, arme sus imanes sobre los discos y denle varias vueltas con el alambre.
VACIADO DEL ROTOR
Antes de comenzar, verifique que todo está listo:
-
Los moldes están listos y están recubiertos de una capa de silicona.
-
Los imanes y los discos están limpios (No grasa).
-
Tiene 16 tiras de fibra para colocar entre los imanes.
-
El alambre de acero inoxidable está en su sitio.
-
La plantilla de ubicación de los imanes está lista.
Las cantidades de resina que indicamos con suficientes para dos rototes.


· Coloque los cuatro pernos en los cuatro agujeros del molde exterior. Coloque ahora un disco de acero entre ellos. Coloque el molde inferior sobre el disco verificando que el bisel le permitirá extraer este molde al final.
· Mezcle 200 gramos de resina con 3 cc de catalizador y pinte el disco de acero. Mezcle 100 gramos de talco al resto de la resina y vacíelo dentro del molde hasta que quede a nivel del disco de acero..
· Coloque la plantilla de los imanes en los pernos y coloque los imanes dentro de esa plantilla. Verifique por última vez su situación N, S, N, S.
· Retire la plantilla para usarla en el otro rotor. Recuerde el posicionamiento de los imanes en ese rotor, que deberá ser S, N. S, N, etc., de manera que ambos rotores al ser fijados se atraigan mutuamente. Si no es así, su alternador no funcionará.
· Coloque ahora el espaciador y apriételo con tuercas.
· Mezcle 500 gramos de resina con 7cc de catalizador. Añada 300 gramos de talco. Coloque pequeñas tiras de fibra entre los imanes y en sus extremos. Añada resina hasta que bañe la fibra y elimine las burbujas de aire.
· Coloque el anillo de alambre de acero inoxidable alrededor de los imanes y no permita que caiga al pie de los imanes sino que repose sobre la fibra. No mueva los imanes.
· Mezcle 500 gramos de resina con 7cc de catalizador. Añada 300 gramos de talco. Llene todos los espacios hasta que la resina alcance el tope del molde.
· Déjelo reposar hasta que fragüe. Tenga paciencia al sacar el rotor de su molde. No dañe ni uno ni otro. Golpee el molde, no el rotor.

Cuatro etapas del procedimiento de vaciado del rotor.
BALANCEO DEL ROTOR.
Cada rotor debe estar balanceado o el GIP vibrará al girar. Todo el conjunto debe ser balanceado al final debido a que los rotores pueden no haber quedado exactamente centrados.
Para balancear un rotor, fíjele la plantilla del DCP empleando cuatro pernos y proceda de la siguiente manera:

Si el rotor se mantiene a nivel, está balanceado. Si no, añádale pequeños pasos de manera de lograrlo. Estos pueden ser pequeños trozos de perno insertados en agujeros en la resina Como otra opción, puede sacar pequeños trozos de resina de entre los imanes para hacer esas áreas más livianas..
TOPE Y MUNICIONERA.

El tope se fabrica con un trozo de tubo de hierro cuadrado de 50x25x4 de 380mm de largo. Márquele el centro exacto de una de las caras y del mismo mada márquele cuatro puntos para agujeros de 8mm. Siga las explicaciones que le dimos al fabricar la plantilla del estator. Puede usar esa plantilla para marcar y perforar los agujeros. El agujero central es de 25mm (O del diámetro del eje). Todos los agujeros deben ser muy precisos.
Suelde el eje en el agujero de 25 mm del tope. Este eje debe quedar a 90 grados del plano del tope.
El espaciador y la municionera (Preferentemente de cojinetes cónicos) se coloca en el eje. No olvide engrasarla.


· Corte cuatro trozos de barra roscada de 10mm de 200mm de largo. Estos se usarán como pernos para fijar los rotores al espaciador. Las aspas de la turbina también si fijarán a estos pernos.

· Deslice los pernos a través de los agujeros del espaciador desde su frente.

· Ponga una tuerca en el extremo de cada perno de modo que el extremo trasero del rotor se fije a la pestaña del separador. La tuerca exterior del perno debe ser protegida con algún elemento antioxidante (Pintura, sellador).

-
Coloque el tope en una prensa con el eje hacia arriba. Coloque el espaciador sobre el eje. No martille sobre el rotor. Asegure el espaciador al eje con una tuerca y una cupilla. No apriete las tuercas en exceso. Coloque un guardapolvo sobre el extremo del espaciador.
-
Gire el rotor. Sus caras deben estar a la misma altura, más o menos 5mm. Si no es así use pequeños espaciadores entre le espaciador y el disco para ajustar esta altura.
-
Con un nivel, nivele el tope en la prensa.
-
Tome el estator y colóquele una tuerca de 8 mm en cada perno de soporte. Lleve estas tuercas hasta el final.
-
Coloque el estator sobre el rotor trasero y fije sus pernos de soporte en los agujeros del tope. Coloque m{as tuercas a los extremos de los pernos

-
Baje el estator lentamente y manténgalo a nivel. Oirá un ruido cuando el imán más alto toque el rotor.
-
Eleve el estator una distancia de 1 mm con las tuercas que colocó en los cuatro pernos.
-
Colóquele arandelas a los pernos de 10 mm que sostienen los rotores.
-
Use siempre el mismo número de tuercas y arandelas en cada perno. Puede que sean suficientes seis tuercas y dos arandelas.
-
Si el rotor frontal está a una distancia menor de 1 mm del estator, añada arandelas para alejarlo. Si está muy distante, retire arandelas. Para determinar cuántas arandelas son precisas es necesario quitar arandelas hasta que rotor toca el estator. Entonces se añaden las arandelas para lograr la distancia deseada de 1mm.

PARTES ELECTRICAS.
La sección 7 explica cómo conectar el rectificador al estator. Recomendamos usar dos rectificadores de una fase. Estos vienen en dos bloques de 30 x 30 mm.

Los terminales positivos se conectan al terminal positivo de la batería (Generalmente están en ángulo recto respecto de los demás terminales). Los terminales negativos se conectan al términal negativo de la batería. El resto de los terminales son de AC para ser conectados al estator. Probablemente sólo será necesario usar tres de esos terminales de acuerdo con la velocidad de giro que disponemos, (Ver sección 7).
Los conectores son útiles para hacer conexiones a las pestañas de los rectificadores, aunque pueden hacerse soldaduras. No sobrecaliente esas pestañas al soldar. Atornille los rectificadores al disipador de calor, que puede ser parecido al que mostramos, aunque cualquier pedazo o pedazos de aluminio de 250 gramos nos servirá. Las conexiones deben quedar protegidas del agua y los elementos.

Dos rectificadores
Verifique que el GIP no tiene fallas. Es mejor corregir cualquier error ahora y no después que lo hayamos montado en su torre.
Pruebas mecánicas.
Monte el tope verticalmente en una prensa. Los rotores pueden girar libremente. El eje está horizontal. Los cables no se tocan creando cortocircuitos. Denle un impulso a los rotores y escuche por ruidos. No debiera haber ninguno. Debiera rotar y detenerse gradualmente. Si se detuviera muy rápidamente podría deberse a una falla eléctrica o a que las municioneras han quedado excesivamente apretadas.
Tome el estator con ambas manos y empuje un lado hacia delante y el otro hacia atrás mientras gira. No debe tocar el rotor. Si lo toca deberá desarmar la unidad y rearmarla para eliminar esta condición proveyendo más espacio entre el estator y uno o ambos rotores.
Ponga uno de los pernos del rotor en la posición de las 3 de la tarde del reloj. Cuelgue un pequeño objeto que pese aproximadamente 100 gramos (Una o dos tuercas) de ese perno. El rotor debe bajar. Si no lo hace es posible que las municioneras estén o muy apretadas o excesivamente engrasadas.

Los rotores ya fueron balanceados en la sección 6. Las aspas de la turbinas también. Cuando se haya armado toda la unidad debe hacerse una verificación final de balanceo de acuerdo al siguiente procedimiento:
Repita el procedimiento de la pesa en todos los pernos de la unidad. Use varios pesos buscando el menor que impulsará el rotor. Este peso debe impulsar el rotor en todas las posiciones o no está balanceada. Fije pequeñas pesas donde sea necesario para lograr el balanceo perfecto.
PRUEBAS ELECTRICAS
Prueba de la conexión de las bobinas.
Si para estas pruebas se pudiera disponer de un multímetro estaríamos en una situación ideal. Es sin embargo posible efectuar algunas pruebas básicas con un bombillo de linterna de 3 voltios.
-
Conecte los cables 1B al 4A, el 2B al 5A y el 3B al 6A (Conexiones en serie de pares de bobinas que están en fase).
-
Fije el multímetro (Si tiene uno) a "10VAC"
-
Conéctelo, o en su defecto el bombillo, a los cables 1A y 4B.

-
Rote el GIP lentamente a mano, aproximadamente a una vuelta por segundo.
-
El medidor debe indicar cercado a dos voltios o el bombillo debe parpadear.
-
Repita esta prueba con los pares de cables 2A y 5B y 3A y 6B. En todos los casos el resultado debe ser el mismo.
Si no hay lectura, o ésta es muy baja verifique que la conexión de la serie es correcta (1B-4A, 2B-5A, 3B-6A). Si la falla continúa es posible que una bobina haya sido colocada al revés o invertida. Esto puede ser verificado así:

Conecte los terminales 4B-2A y 5B-3A como indica el diagrama verifique 1A y 6B. NO DEBIERA HABER SINO UN MINIMO VOLTAJE. Si hubiera voltaje o el bombillo encendiera, invierta las conexiones (A por B) y observe si el voltaje cae. Al localizar la bobina que falla haga ese cambio y repita toda su prueba hasta ahora. Hay la posibilidad de que en esta prueba se detecte un leve voltaje. Si es mayor a 1 voltio, de deberá tener mayor cuidado al fabricar un futuro estator colocando las bobinas a distancia exacta cada una de ellas en el mismo.
PRUEBA DE SALIDA DE DC
Al concluir las pruebas y resultar todas ellas satisfactorias, conecte el rectificador como se indica:

Conecte los terminales 1A, 2A y 3A juntos. Conecte los terminales 4B, 5B y 6B a cualquiera de los terminales de los rectificadores identificados con la letra "S". Esta es la configuración "estrella". Conecte un bombillo y si es posible un multímetro a los terminales de salida.
Gire el rotor a mano a una revolución por segundo. El multímetro debe indicar v voltios DC (O 3 voltios al bombillo). El bombillo no debe parpadear. Si ello ocurre, existe una conexión errónea o un rectificador dañado. Revise las conexiones o pruebe con otro rectificador. Otro método de verificación es crear un cortocircuito conectando los cuatro cables del rectificador. Trate de girar el GIP. Debe ser duro pero suave al girar. Si tiembla hay una falla.
USO DE UN RELE PARA CAMBIAR DE ESTRELLA A DELTA.
Si no es necesario efectuar cambios entre alta y baja velocidad el GIP funcionará, aunque se inducirán pequeñas ineficiencias. Para resolverlas hay dos opciones:
-
Si sólo se esperan vientos suaves basta con emplear la conexión estrella antes descrita.
-
Si se esperan corrientes de alta velocidad use alambre 17AWG (1.2mm) y haga sus bobinas de 200 vueltas. Ahora se puede conectar un grupo de ellas en la configuración estrella y otro en la configuración delta. Como ahora se necesitan seis terminales de AC en los rectificadores ahora necesitamos tres de ellos.

CONEXIÓN ESTRELLA/DELTA

El cable a la batería puede ser de trifásico de AC ó DC. Si el rectificador se monta en la torre deberá ser DC, que es la corriente que llevará a la batería. Pero si el rectificador está en la casa deberá ser AC. Las diferencias de eficiencia de cada cable son menores.
Pero a 12 voltios el cable debe ser grande aún a solo 15 amperios. Para distancias de 20 metros debe usarse 10AWG. De lo contrario el cable se calentará disipando la energía.
SEGURIDAD
No hay peligro de descargas desde una batería de 12V. Pero si el generador está desconectado de la batería y girando rápidamente podemos estar hablando de hasta 50 voltios, que a 12 amperios son 600 vatios. Esto si proporciona un buen golpe. No haga funcionar el generador a alta velocidad si no le tiene una batería conectada.
Nunca está demás colocar fusibles desde el generador hasta la batería.
CARGA DE LAS BATERIAS
Las baterías de ácido y plomo deben mantenerse cargadas. En el caso de un sistema de viento habrá que esperar a que éste venga para cargar las baterías. Tenga el cuidado de no descargar sus baterías totalmente.
Cargar las baterías muy rápidamente también las daña. Es preferible cargarlas lentamente por un periodo prolongado. Vigile el estado de carga de sus baterías. Si su voltaje a m{as de 11.5 voltios están muy descargadas. Por el contrario, si la carga supera 14 voltios están cargadas en exceso. Descárguelas. Si no tiene un instrumento de medición de voltaje, use las siguientes reglas:
-
Las luces opacas nos dicen que las baterías están descargadas. Use poca electricidad.
-
Las luces muy brillantes indican que las baterías tienen exceso de carga. Use mucha electricidad.
-
Para consumir baterías haga que sus vecinos les traigan sus baterías a cargar.
Para obviar el problema de exceso de carga en las baterías existen unos reguladores de voltaje como los de los vehículos que se insertan en el circuito.
Para la obtención de corriente AC de 120 voltios en cantidades limitadas de las baterías (Que sólo almacenan corriente DC), es necesario obtener un pequeño convertidor que se conecta directamente a ella.
Estos convertidores se consiguen con salidas de voltaje de varios rangos. A seguidas describimos tres tamaños.
Modelo
|
Continuo
|
Pico
|
Conector
|
# salidas
|
Costo Aprox.
|
PC140
|
140 Watts
|
200 Watts
|
Encendedor de carro
|
1
|
$45
|
PC300
|
300 Watts
|
500 Watts
|
Encendedor de carro
|
2
|
$80
|
PC500
|
500 Watts
|
800 Watts
|
Ganchos
|
2
|
$120
|
Tomado y traducido de (http:/www.scoraigwind.co.uk) de Dr. Hugh Pigott.
Guide To Wind Energy? (Manual de Energía Eólica) J.M. ESCUDERO LOPEZ.
Energy of Powerful Wind (?Energía Eolica). Antonio Colmenar, Manuel Alonso Castro Gil.
Fundamentos básicos de la electrónica de potencia, Salvador Seguí Chilet.
Energía eólica práctica, Paul Gipe, Tupac Canosa, Conrado Moreno.
|